Modeling can be a powerful tool for designing various aspects of the heat treatment process. One application is to design the heating time required for complex geometries to reach the furnace temperature.
Cylinder Geometry
OD: 100 mm
Furnace Temperature: 950 °C.
By analyzing the core temperature history from the model, we can determine the optimal time required to reach the target temperature.
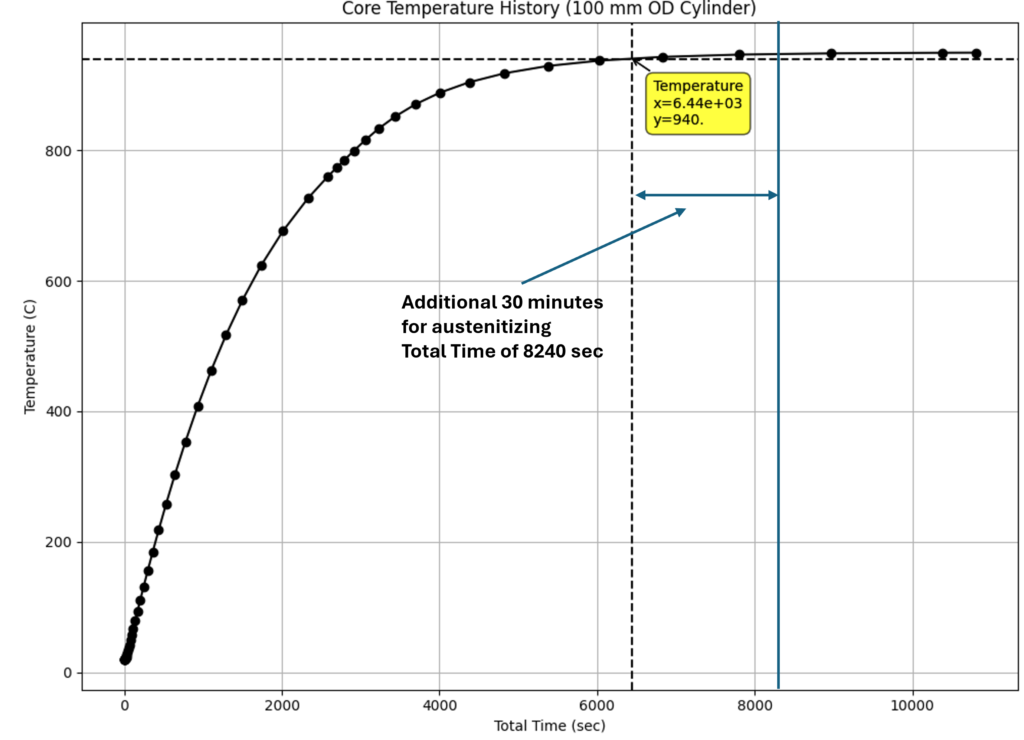
If we set a target temperature of 940 °C for the core, the required time it takes to reach the target temperature for this geometry is about 1.79 hours (107 minutes). After adding an additional 30 minutes for austenitizing, the total heating time comes out to approximately 2.29 hours (137 minutes). Modeling the core temperature of any geometry can greatly optimize the heating process by saving valuable time.